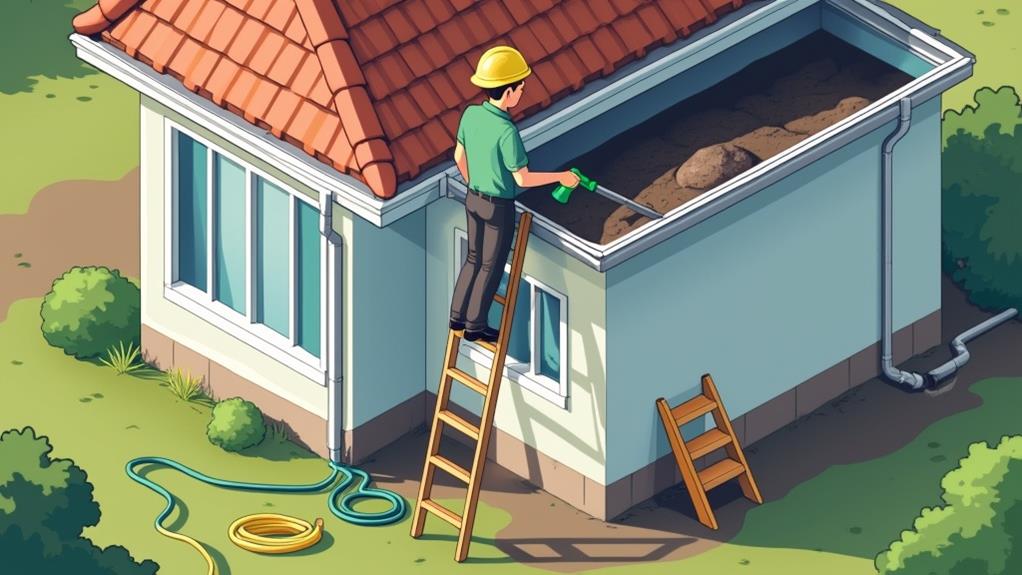
Pre-Installation Gutter Inspections: What to Expect From Industrial Gutters MA
November 26, 2024
When preparing for new industrial gutter installations in Massachusetts, you can expect a thorough pre-installation gutter inspection to guarantee your gutter system’s durability and efficiency. This process involves a detailed assessment of your roofline, fascia, and soffits to identify potential issues such as damage, rot, or improper slope. Inspectors will use advanced tools like laser levels and moisture meters to evaluate the existing conditions, measure the building precisely, and plan for proper water drainage. They will also simulate heavy rain to test the system’s performance and identify weak points. This inspection helps prevent costly rework, guarantees peak performance, and tailors the design to your building’s specific needs. By understanding these steps, you’ll be better equipped to guarantee your gutters function effectively from the start, and continuing to explore this topic will provide even more insights into maintaining a robust gutter system.
Pre-Installation Gutter Inspections: What to Expect from Industrial Gutters MA
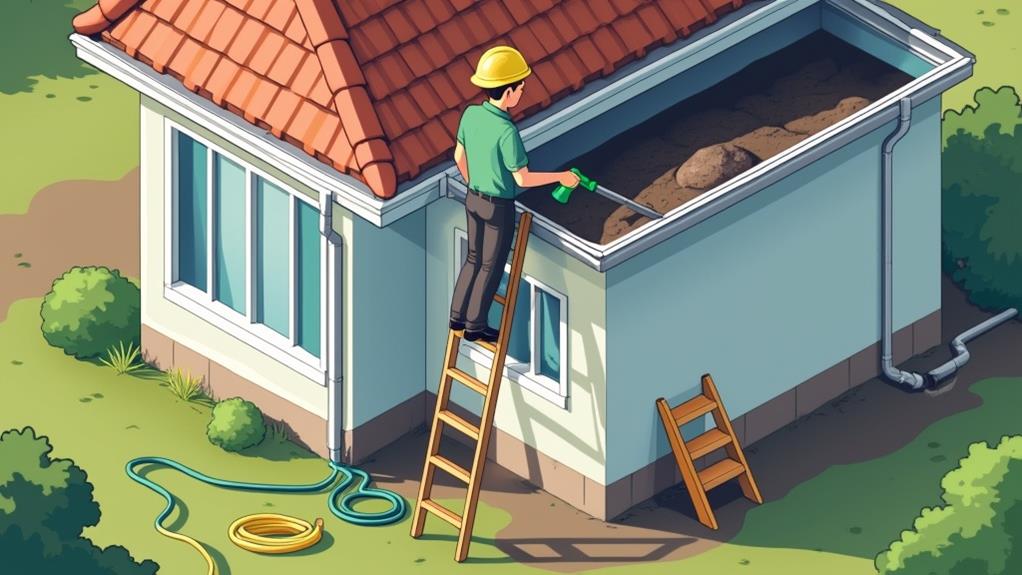
When considering pre-installation gutter inspections, you need to understand what the process entails and how it benefits your building. Key steps in a pre-installation inspection include a visual assessment of the rooflines, fascia, and soffits, as well as an evaluation of the building’s specific drainage requirements. Industrial Gutters MA uses advanced tools like laser levels, moisture meters, and water flow simulations to guarantee a tailored and efficient gutter system.
What Are Pre-Installation Gutter Inspections?
Pre-installation gutter inspections are vital for confirming that your gutter system is both durable and efficient, tailored specifically to your building’s unique needs. These inspections involve a thorough assessment of several significant components to guarantee the new gutter system will function at peak performance.
Here are the key aspects of a pre-installation gutter inspection:
1. Assessing Existing Conditions
Inspect the old gutters and downspouts to identify any damage or issues that need to be addressed before the new installation. This includes checking for rotted boards, unusable pieces of fascia, and other potential problems behind the old gutters[1].
2. Measuring and Preparing
Take precise measurements of your home to determine the exact placement and requirements for the new gutters. This step is vital for confirming the gutters are correctly angled and directed towards the downspouts, facilitating proper water drainage[1].
3. Inspecting Roofline and Fascia
Examine the roofline, fascia, and soffit areas for any signs of water damage, rotting wood, or other structural issues. This guarantees that the new gutters will be supported by a stable and intact structure, preventing future problems[3][5].
Key Steps in a Pre-Installation Inspection
When preparing for a gutter installation, you need to conduct a thorough pre-installation inspection. Start by evaluating the roofline, paying attention to slopes, edges, and architectural features to guarantee the gutters will be properly aligned and sloped for effective water flow. Next, inspect the fascia and soffit to verify their structural stability, and then analyze the drainage requirements to calculate the correct water runoff and gutter sizing, including planning downspouts to prevent pooling and foundation damage. Finally, perform a structural check to evaluate the reinforcements and load-bearing capability of the existing framework.
Roofline Assessment: Slopes, Edges, and Architectural Features
During a pre-installation gutter inspection, evaluating the roofline is essential for guaranteeing a gutter system that is both durable and efficient. You need to assess the slopes, edges, and architectural features of your roof.
Roofline Assessment
Feature | Consideration |
---|---|
Slope | Guarantee a minimum slope of 1/16-inch per foot towards downspouts to prevent water accumulation[2][3]. |
Edges | Check for even alignment and secure attachment points for gutters[5]. |
Architectural Features | Note any complex designs, such as valleys or multiple roof levels, which may require specialized gutter solutions[3]. |
This assessment helps tailor the gutter system to your building’s unique needs.
Fascia and Soffit Inspection: Ensuring Structural Stability
To guarantee the structural stability of your gutter system, it’s crucial to conduct a thorough inspection of the fascia and soffit.
Inspection Checklist
Component | Function | Signs of Damage | Maintenance Tips |
---|---|---|---|
Fascia | Supports gutters, protects roof | Cracking, water damage | Regular inspections, cleaning |
Fascia | Aesthetic finishing edge | Rot, blistering | Confirm proper gutter installation |
Soffit | Attic ventilation, pest protection | Holes, water seepage | Clean gutters, inspect for pests |
Soffit | Aesthetic finish | Mold, structural flaws | Check for animal infestations |
Confirm your fascia and soffit are in good condition to prevent water damage and structural issues[1][3][5].
Drainage Analysis: Calculating Water Runoff and Gutter Sizing
Calculating water runoff and determining the appropriate gutter sizing are critical steps in a pre-installation gutter inspection. You need to assess the roof’s surface area, pitch, and the average rainfall in your area to calculate the water volume. Use tools like laser levels and water flow simulations to guarantee the gutters can handle the runoff efficiently. Proper sizing prevents overflow and guarantees peak drainage, protecting your home from water damage[1][3][5].
Downspout Planning: Preventing Pooling and Foundation Damage
When planning downspouts as part of a pre-installation gutter inspection, your primary goal is to prevent pooling and potential foundation damage. Make certain downspouts are positioned to direct water at least 3-4 feet away from the foundation. Check the slope and alignment of gutters to make certain water flows freely towards downspouts. Use splash blocks or extenders to manage water flow and prevent erosion around the foundation[3][5][1].
Structural Check: Reinforcements and Load-Bearing Capability
After verifying downspouts are correctly positioned to prevent pooling and foundation damage, the next step in a pre-installation gutter inspection involves a thorough structural check of the reinforcements and load-bearing capability of your gutter system. You need to inspect the hangers, spikes, and fascia boards to verify they are secure and can support the weight of gutters, debris, and water. Check for any signs of sagging, loose fasteners, or damage that could compromise the system’s integrity[1][5][3].
Tools and Techniques Used During Inspections
When conducting a pre-installation gutter inspection, you will use several vital tools to guarantee accuracy and thoroughness. Laser levels help you assess the roof slopes and alignment, confirming the gutters will be installed at the correct angle for maximum water flow. Moisture meters are essential for detecting any hidden damage or potential issues with the fascia and soffits, while inspection cameras, such as telescopic cameras or drones, allow you to inspect hard-to-reach areas without the need for ladders. Additionally, water flow simulations can be used to test how the gutter system will perform under heavy rain conditions, helping you enhance the system’s design[1][3][5].
Laser Levels for Roof Slopes and Alignment
To guarantee proper gutter installation, using laser levels is essential for accurately evaluating and setting the slopes and alignment of your roof.
Here are key steps to use laser levels effectively:
- Set Up and Level: Place the laser level on a tripod, confirming it is horizontally leveled and stabilized.
- Mark the Slope: Use the laser to mark a line along the fascia, adjusting the beam to achieve the desired slope, typically a 2-3% grade.
- Verify Alignment: Employ a laser detector to check the alignment and slope at multiple points, confirming the gutter will drain properly.
This method guarantees precise and efficient gutter installation.
Moisture Meters for Detecting Damage
During pre-installation gutter inspections, using moisture meters is essential for detecting hidden damage and ensuring the integrity of your building’s structure. These meters measure moisture content in materials like wood, drywall, and roofing, helping you identify potential issues such as mold, rot, and decay. They can operate in two main modes: pin-type, which measures electrical resistance, and pinless, which uses electromagnetic waves to assess moisture levels without causing damage[1][5][3].
Inspection Cameras for Hard-to-Reach Areas
After using moisture meters to detect any hidden damage, the next step in pre-installation gutter inspections involves utilizing inspection cameras to examine hard-to-reach areas of your gutter system. These cameras, such as the skyVac® Gutter Inspection Camera or the SurveyCam, allow you to view live, high-quality images from the ground, ensuring a thorough assessment of rooflines, gutters, and drainage systems without the need for ladders or other risky equipment[1][3][5].
Water Flow Simulations for Heavy Rain Conditions
When planning a gutter system, simulating water flow under heavy rain conditions is essential for ensuring the system’s durability and efficiency. Use a hose to mimic rainfall and observe how water flows through the gutters. This method helps identify potential leaks, areas of pooling, and misalignments, ensuring that the gutters can handle heavy rain without overflowing or causing damage[1][5][3].
Benefits of Pre-Installation Inspections
Pre-installation gutter inspections are essential for identifying potential weak points in your gutter system, allowing you to address them before they become major issues. By conducting these inspections, you can avoid the cost and hassle of rework, optimizing the system’s performance from the outset. This approach also enables the creation of custom solutions tailored to your building’s unique needs, ensuring a durable and efficient gutter system that withstands various weather conditions and maintains your home’s integrity[1][3][5].
Preventing Future Issues: Identifying Weak Points
To guarantee your gutter system functions efficiently and lasts long, identifying weak points before installation is essential. Here are key areas to focus on:
- Roofline Integrity: Check for any sagging or uneven sections that could affect water flow.
- Fascia and Soffit Condition: Ascertain these areas are secure and free from damage to prevent water infiltration.
- Drainage Pathways: Verify that downspouts are clear and directed away from the foundation to prevent water accumulation.
This thorough inspection helps prevent future issues like clogs, leaks, and water damage[1][5][3].
Cost Efficiency: Avoiding Rework and Optimization
How can you guarantee that your gutter system is not only effective but also cost-efficient from the outset? Conducting a thorough pre-installation gutter inspection helps avoid costly rework by identifying potential issues early. This includes checking the slope and alignment of gutters, ensuring secure hangers and fasteners, and testing downspouts to prevent future clogs and leaks. Regular inspections also optimize system performance, reducing long-term maintenance costs[1][5][3].
Custom Solutions for Industrial Needs
When installing a gutter system for an industrial building, it is essential to tailor the design to the unique needs and challenges of the structure. Consider the roof’s size, slope, and average rainfall in the area to determine the ideal gutter size and downspout placement. For industrial buildings, larger gutters (up to 8 inches) and materials like galvanized steel or aluminum are often necessary to handle heavy water volumes and withstand external damage[3][4].
Industrial Gutters MA’s Specialized Approach
When considering pre-installation gutter inspections with Industrial Gutters MA, you can expect an expert assessment by trained professionals who will thoroughly evaluate your building’s unique needs. This process involves customer collaboration to provide clear findings and present various options, ensuring you understand the best solutions for your property. Industrial Gutters MA specializes in tailored solutions using seamless systems and advanced technologies like RainPro and MasterShield, which are designed to handle the challenges of heavy Northeast weather and complex industrial building designs.
Expert Assessment by Trained Professionals
Expert assessment by trained professionals is the cornerstone of a successful pre-installation gutter inspection. When you work with Industrial Gutters MA, you can expect thorough evaluations from experts who inspect your rooflines, fascia, soffits, and drainage requirements. They use advanced tools like laser levels and moisture meters to guarantee your gutter system is tailored to your building’s unique needs and can handle heavy Northeast weather conditions. This expert assessment helps prevent future issues, optimizes system performance, and guarantees long-term satisfaction.
Customer Collaboration: Clear Findings and Options
During the pre-installation gutter inspection process, clear communication and customer collaboration are essential for guaranteeing that the gutter system meets your specific needs and expectations. You will be presented with clear findings, including assessments of your rooflines, fascia, soffits, and drainage requirements. You will also be given options for materials and technologies, such as RainPro and MasterShield, along with explanations of their benefits and any necessary adjustments to guarantee peak performance. This collaborative approach ensures that you are fully informed and satisfied with the final installation.
Tailored Solutions with Seamless Systems and MasterShield
In the process of designing a tailored gutter system, Industrial Gutters MA focuses on integrating seamless systems and advanced technologies like MasterShield to confirm your building’s unique needs are met. They use high-quality materials, such as aluminum, copper, and stainless steel, to guarantee durability against heavy Northeast weather. MasterShield gutters prevent clogs, optimizing water flow and system performance with a lifetime warranty[2][5].
Common Findings During Inspections
During pre-installation gutter inspections, you may encounter several critical issues that need addressing. For instance, you might find fascia boards that require replacement due to water damage or rot, indicating poor drainage and the need for immediate repair. Additionally, you may need to make roofline adjustments to optimize drainage, and identify areas prone to clogs and debris accumulation, such as sections where leaves and twigs tend to gather[1][3][5].
Fascia Boards Requiring Replacement
When preparing for a gutter installation, inspecting the fascia boards is a critical step that cannot be overlooked. You need to check for signs of rot, cracks, splits, or holes, as these indicate the need for replacement. Improperly installed or clogged gutters can cause water damage, leading to fascia board deterioration. If damaged, replace the boards before installing new gutters to prevent further water infiltration and structural issues[1][5][3].
Roofline Adjustments for Drainage Optimization
To confirm your gutter system functions at its best, adjusting the roofline for drainage is an important step in pre-installation gutter inspections. You need to make sure the gutters are properly sloped to direct water efficiently toward the downspouts. Incorrect sloping can lead to water pooling, overflow, and structural damage. Adjusting gutter hangers and supports to maintain the correct slope is vital for effective water management and preventing future issues[2][3][5].
Evidence of Water Damage or Poor Drainage
Evidence of water damage or poor drainage is a critical aspect to identify during pre-installation gutter inspections. Look for signs such as peeling paint, mold, or mildew on the exterior of your home. Check for water stains on the roof cornices and underside of the roof, which can indicate ice dams or leaks. Also, inspect for sagging gutters, disconnected downspouts, and debris accumulation, as these can cause water to overflow and seep into the foundation[1][5][3].
Areas Prone to Clogs and Debris
During pre-installation gutter inspections, identifying areas prone to clogs and debris is essential for ensuring the longevity and efficiency of your gutter system. Here are key areas to focus on:
- Tree Debris: Leaves, twigs, and branches from nearby trees can clog your gutters, especially during autumn[3][5][1].
- Downspouts: Regularly inspect downspouts for obstructions like leaves, twigs, or other debris that may block water drainage[2][4][1].
- Overhanging Branches: Trim back branches that hang over the roofline to minimize debris buildup and reduce the need for frequent gutter cleaning[2][3][5].
Challenges Addressed by Pre-Installation Inspections
When preparing for gutter installation, especially in the Northeast where heavy snow and rain are common, pre-installation inspections are vital. You need to guarantee your gutters are pitched correctly to manage water flow efficiently and prevent issues like standing water, which can lead to structural damage and foundation problems[2][5][4].
For industrial buildings, specialized planning is essential to account for unique features such as larger roof areas, specific drainage requirements, and the condition of the fascia and soffits, which must be in good condition to support the gutters[3][4].
Managing Heavy Snow and Rain in the Northeast
Managing heavy snow and rain in the Northeast is essential for the longevity and efficiency of your gutter system. Here’s how pre-installation inspections address these challenges:
Key Considerations
- Proper Slope: Verify gutters slope correctly (about 1/4 inch per 10 feet) to prevent water pooling and ice formation[1][3][5].
- Adequate Size: Choose gutters and downspouts that can handle the volume of water and snowmelt, typically larger sizes in the Northeast[1][3].
- Durable Materials: Select materials and systems, like RainPro and MasterShield, that are resilient to heavy snow and rain[1][5].
Specialized Planning for Industrial Building Features
Pre-installation gutter inspections for industrial buildings involve a meticulous assessment of the building’s unique features to assure a gutter system that is both durable and efficient. You will need to evaluate the roofline, fascia, and soffits to assure proper alignment and drainage. Check for any structural integrity issues, such as sagging or rust, and verify that the gutter slope is adequate to prevent standing water[1][3][5].
Why Pre-Installation Inspections Are Essential
When planning to install a new gutter system, pre-installation inspections are essential for ensuring the longevity and efficiency of your gutters. These inspections help you reduce the risk of gutter failure by identifying and addressing potential issues such as improper slope, blockages, and structural damage before they become major problems. By conducting thorough assessments of your rooflines, fascia, soffits, and drainage requirements, you can prolong the lifespan of your gutters and provide yourself with precision and peace of mind.
Reducing Risk of Gutter Failure in Industrial Settings
To guarantee the longevity and efficiency of your industrial gutter system, it is essential to conduct thorough pre-installation inspections. Check for sagging gutters, loose or missing brackets, and signs of damage from the ground before ascending ladders[4][5][3]. Clean the gutters to reveal underlying issues, inspect for leaks and holes, and verify proper slope and drainage to prevent water pooling and structural damage[1][4][5].
Prolonging Gutter Lifespan with Proactive Solutions
Ensuring the longevity and efficiency of your industrial gutter system starts with a thorough pre-installation inspection. You need to inspect the fascia board for any signs of rot, damage, or instability, as these can compromise the gutter hangers’ support. Use advanced tools like laser levels to maintain the correct slope, preventing water backup and structural damage. Regular inspections and maintenance, such as clearing debris and checking for clogs, are essential for ideal performance and extending the gutter system’s lifespan.
Providing Precision and Peace of Mind
A thorough pre-installation gutter inspection is essential for establishing a durable and efficient gutter system tailored to your building’s unique needs. You will benefit from a detailed assessment of your rooflines, fascia, soffits, and drainage requirements. Using tools like laser levels and water flow simulations, the inspection guarantees peak system performance, preventing future issues and providing long-term satisfaction with lifetime warranties.
Post-Inspection Recommendations
After a pre-installation gutter inspection, you should focus on repairing any damage to the fascia and soffits to guarantee the longevity of your gutter system. Installing seamless systems can minimize weaknesses and potential leak points. Additionally, consider adding debris guards like MasterShield to prevent clogs and maintain ideal water flow[1][3][5].
Repairing Fascia and Soffits for Longevity
When conducting a thorough gutter inspection, repairing the fascia and soffits is essential for the longevity and integrity of your gutter system. Check for water damage, such as rotting wood or peeling paint, and make certain these areas are secure. Loose or damaged hangers and fasteners can compromise the stability of your gutters, so tighten or replace them as needed. Addressing these issues prevents further damage and guarantees peak gutter performance[3][4][5].
Installing Seamless Systems to Minimize Weaknesses
Installing seamless gutter systems is a crucial step in ensuring the durability and efficiency of your gutter system, and it begins with a thorough pre-installation inspection. Seamless gutters, made from a continuous piece of material, minimize weaknesses by eliminating joints where leaks and clogs often occur. This design reduces maintenance, prevents debris buildup, and enhances the aesthetic appeal of your home, ensuring a long-lasting and effective gutter system[1][3][5].
Adding Debris Guards like MasterShield
Adding debris guards like MasterShield to your gutter system is an essential step in maintaining its efficiency and longevity. MasterShield’s micro-mesh technology, infused with copper, effectively sheds debris and handles high water volumes. The angled installation and HydroVortex technology guarantee water flows into the gutters while keeping debris out, reducing maintenance and protecting your home from water damage[1][3][5].
Industrial Gutters MA’s Key Differentiators
When considering pre-installation gutter inspections, you can benefit from Industrial Gutters MA’s expertise in several key areas. Their experience with industrial-scale projects in New England equips them to handle the unique challenges of heavy Northeast weather and complex building designs. By using premium materials like RainPro gutters and offering lifetime warranties, Industrial Gutters MA guarantees long-term satisfaction and peak system performance.
Experience with Industrial-Scale Projects in New England
In the heart of New England, where harsh weather conditions and complex building designs are commonplace, Industrial Gutters MA stands out for its expertise in handling industrial-scale gutter projects.
Here are key aspects of their experience:
- Customized Solutions: Tailored gutter systems designed to withstand heavy Northeast weather.
- Advanced Materials: Use of durable aluminum gutters and guards for longevity and quality.
- Comprehensive Inspections: Detailed assessments of rooflines, fascia, soffits, and drainage requirements to guarantee peak performance.
Use of Premium Materials Like RainPro Gutters
As you prepare for the installation of a new gutter system, the choice of materials is as important as the design and installation process itself. Industrial Gutters MA uses premium materials like RainPro gutters, known for their durability and efficiency. These gutters feature a unique design that enhances water flow, reduces clogging, and withstands heavy Northeast weather conditions, ensuring long-term performance and satisfaction.
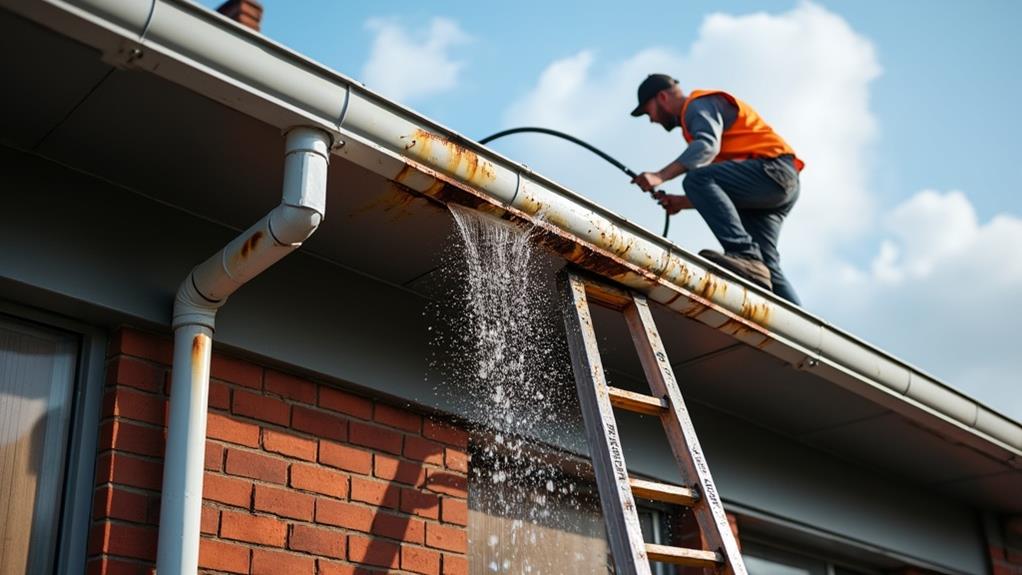
Lifetime Warranties for Long-Term Satisfaction
Assuring your gutter system stands the test of time involves more than just the installation process; it also depends on the assurance of long-term performance through lifetime warranties. With Industrial Gutters MA, you can trust that your gutters are backed by a lifetime warranty, guaranteeing durability and efficiency against ice and snow loads, and other harsh weather conditions. This warranty assures your investment is protected, providing long-term satisfaction and peace of mind.